Since COVID-19 affects lung function, oxygen is essential for the treatment of people with severe cases of the condition. Breathing problems or shortness of breath are among the most prevalent symptoms in COVID-19 patients. Additionally, it impairs the flow of oxygen to numerous bodily areas. As a result, they require oxygen therapy, which can be provided through medical oxygen. The process of respiration, which transports energy from glucose to cells, depends on oxygen. In actuality, oxygen is needed by every cell in our body. When we breathe in air, oxygen atoms travel to our lungs, where they pass through the lung tissue and into our blood. The use of liquid medical oxygen is one method of supplying this oxygen (LMO). LMO was created for use in the human body and is nothing more than high purity oxygen utilized for medicinal therapy.
How Liquid Medical Oxygen Is Produced?
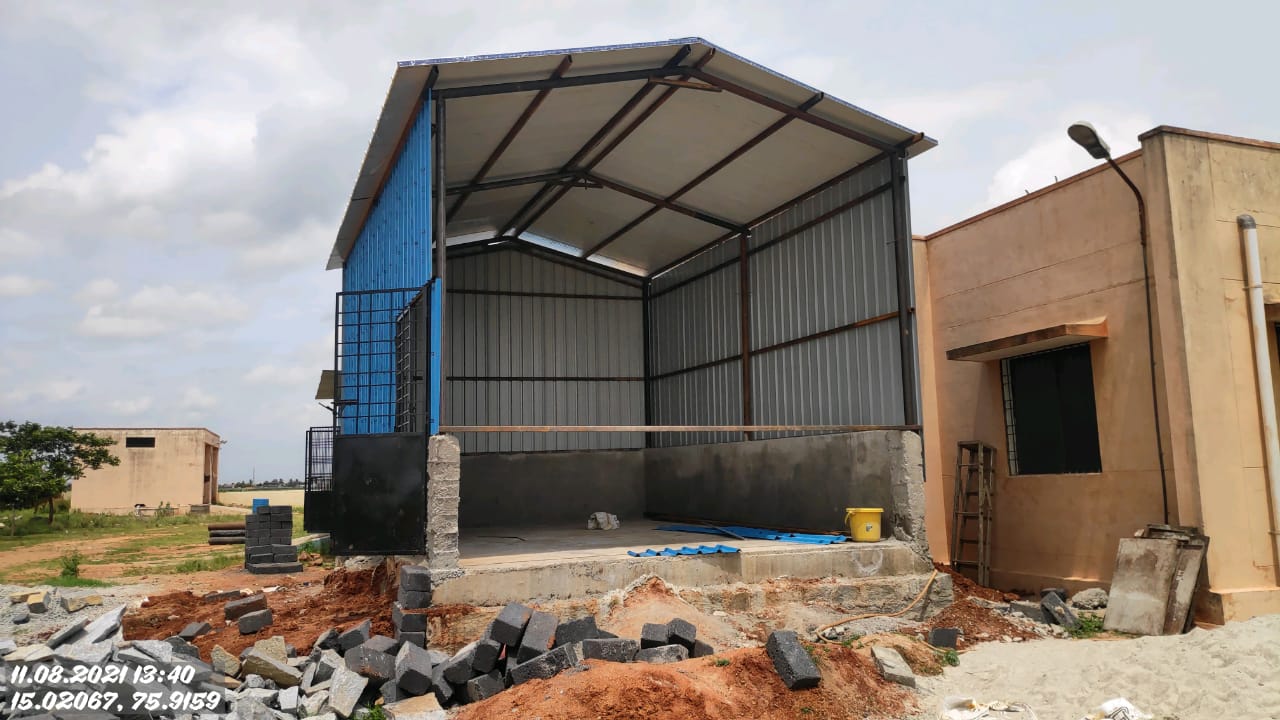
The most popular method of production is the air separation unit, or ASU, which separates oxygen from other gases. Asus are essentially factories that separate huge quantities of gases. With 78 percent nitrogen, 21 percent oxygen, and the remaining 1 percent made up of various gases like argon, carbon dioxide, neon, helium, and hydrogen, they employ a process called fractional distillation to create pure oxygen from atmospheric air. This approach involves chilling gases from the air into a liquid state, separating them into different components, and then extracting liquid oxygen from each component.
First, atmospheric air is chilled to -181°C. Now, oxygen starts to liquefy. Since nitrogen's boiling point is -196°C, it can only exist as a gas. However, since argon has a boiling point that is comparable to that of oxygen (-186°C), a sizeable amount of argon liquefies with oxygen.
The stainless-steel inner vessel and carbon steel outer vessel make up the double-walled Vacuum Insulated Evaporator (VIE). To insulate under a vacuum, non-flammable perlite insulating material must be inserted into the annular area between the vessels. The VIE should be of the self-pressurizing kind, with liquid oxygen partially evaporated through a pressure-building coil by an imported non-ferrous pressure regulator. The LMO tank needs to have a liquid outlet, a gas outlet, and all the essential valves and equipment. Inside the vessel, information such as pressure and LMO level is continuously displayed. The MGPS network is connected to the output from the tank at the MGPS Manifold by a copper line with the appropriate diameter. All building materials and a cleaning procedure appropriate for liquid oxygen of the medical grade must be delivered to the vessel as a functional whole.
Medical oxygen is a colorless, odorless liquid that only solidifies at temperatures between -190 and -183 degrees Celsius. The liquid will transform back into its gaseous molecular state when kept at ambient temperature. The typical packaging for this product is PET bottles, plastic cylinders, or glass jars. The most used type of medicinal oxygen is concentrated oxygen. It is available in higher amounts than ambient air, which contains 21% oxygen. It's also known as 40 volume or 40 percent at times. Patients who have acquired issues breathing due to lung disease utilize this form of medical oxygen.4