PSA Plants are constructed in accordance with specifications that specify a "rated" production capacity. The factory, for instance, is capable of producing 16 cubic metres per hour. As a result, you can compute that 384CM each day equals 24 hours times 16CM per hour. The number of cylinders that can be produced per hour or per day is determined by dividing the total CM per day by the usual size of the cylinder.The number of cylinders that can be produced per hour or per day is determined by dividing the total CM per day by the usual size of cylinder. However, it is unlikely that the plant will run continuously, thus it is reasonable to expect that between 80% and 90% of the rated capacity will really be used. In order to construct a PSA plant taking into account height above sea level and environmental common temperature range, the manufacturer will need to know the location where the plant is to be put.
Let's have a detailed discussion regarding the PSA oxygen plant capacity calculation.
Utilizing PSA (Pressure Swing Adsorption) technology, oxygen gas plants guarantee a constant supply of pure oxygen. With the use of this technology, we can create oxygen gas plants that are hassle-free to operate, extremely cost-effective, and minimal maintenance. Two absorption jars loaded with the most effective zeolite molecular sieves for nitrogen absorption are used by these generators to absorb nitrogen.
Using zeolite molecular sieves, oxygen is separated from other gases, such as nitrogen, in the process of producing oxygen gas from air that has been compressed. Two towers containing zeolite molecular sieves, which absorb nitrogen and then release waste, are used in the procedure. 95 percent pure oxygen is produced. This process switches to the opposite tower when nitrogen in one tower reaches saturation, assisting in the ongoing production of oxygen.
PSA Oxygen Plant Capacity Calculation
1 to 200 Nm3/hr of capacity
Purity 93 minus 2%
2 to 150 Bar g of pressure
All systems are built for autonomous oxygen demand adjustment and unattended operation. The design and instrumentation result in a relatively small plant that is prefabricated, factory-supplied, and assembled on skids. To achieve the appropriate oxygen purity, the startup time is only five minutes. So, depending on changes in oxygen demand, these units can be turned on and off. Very trustworthy for continual, steady functioning with pure oxygen. Plant uptime is always greater than 99 percent. The lifespan of a molecular sieve is anticipated to be 10 years, or the lifespan of an oxygen plant. No replacement charges, therefore.
- Here are some Applications of PSA oxygen plant
- Oxygen bleaching and delignification in the paper and pulp industries
- industries using glass to enrich furnaces
- industries that use oxygen in metallurgy
- furnace enrichment
- Chemical industry for incinerators and oxidation reactions
- Treatment of effluent and wastewater
- Glass shell/color and black-and-white picture tube industry
- Industry for Compact Fluorescent Lamps
- Application of brazing
- to raise fish
- Generation of Ozone
- Enrichment of LPG
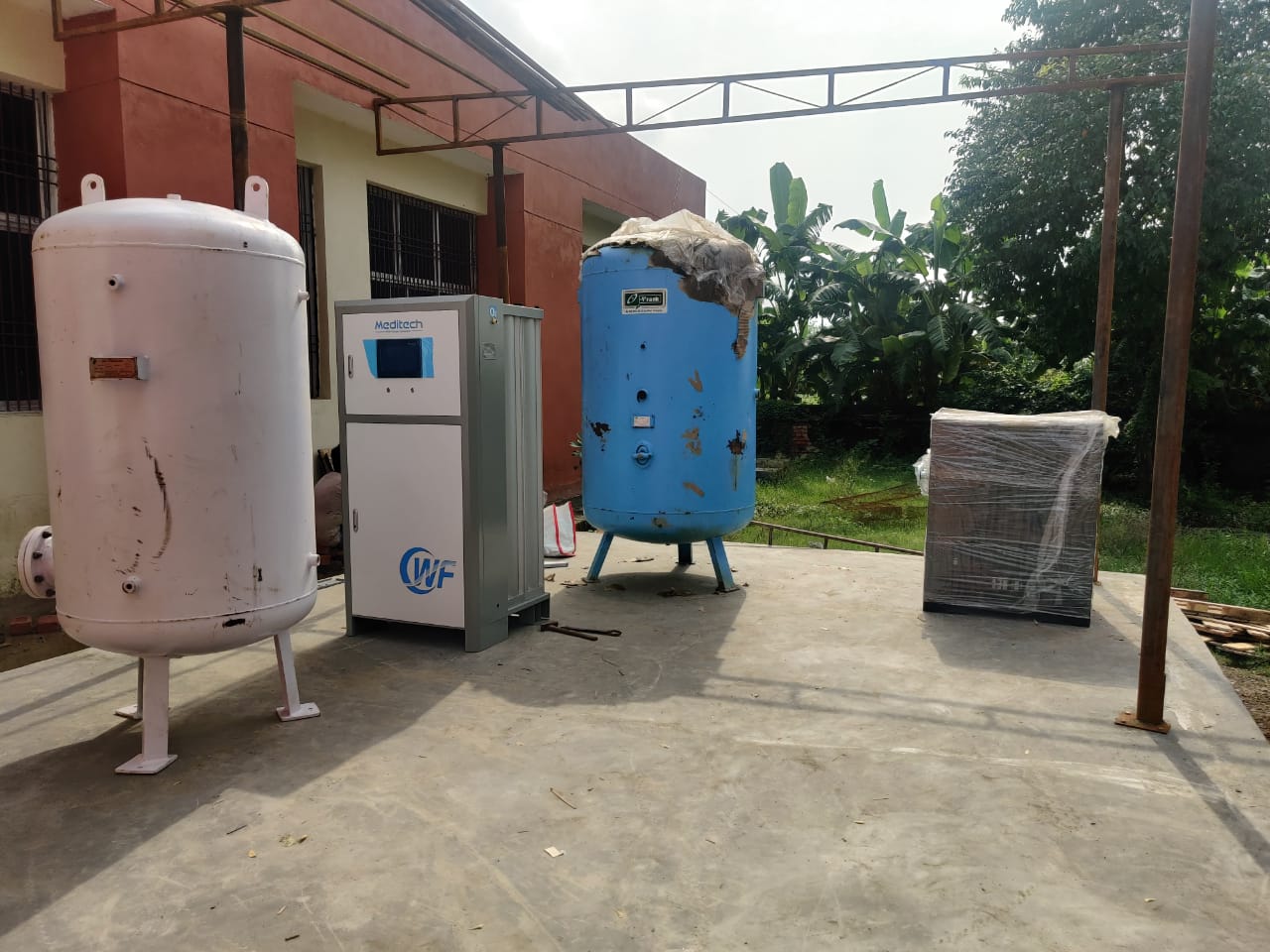
Although the size and capacity of PSA and VSA plants may differ, the fundamental specifications call for an oxygen production purity of 93% to 3% and a continuous output pressure of 50 to 55 psig (US NFPA 99: Health Care Facilities Code), or 400 to 500 kilopascals (kPa) (ISO; piping only).They should be able to supply the required oxygen concentration continuously in conditions of ambient temperature ranging from 10°C to 40°C, relative humidity ranging from 15% to 95%, and elevation ranging from 0 to at least 2,000 metres. They are designed to have a minimum lifespan of 10 years.
In the event of a power outage, a system malfunction, or when the oxygen content falls below 90% purity, a PSA/VSA plant should include both audible and visual alarms. The nominal flow rate for a typical PSA plant is between 0.5 and 150 normal cubic metres per hour (Nm3 /h) or 8 and 2,500 litres per minute (LPM) at 50 pressure. Nominal flow rates for VSA plants range from 52 to 3,155 Nm3 per hour at 5 psig (34.5 kPa).
You can anticipate filling 100–120 cylinders (42L) in a 24-hour period if your oxygen plant has a fill and production rate of 32 cubic metres per hour. Manufacturers provide capacity rates based on hourly or minutely operation. Consider 80 percent of the real world. Since much of Sub-Saharan Africa is higher than 1000 feet above sea level, the plants must be significantly derated there. You should also take into account the size of the cylinders you are utilising because the ideal size for economy and lifespan is in the centre.
The volume of a liquid (usually water) is widely used to describe cylinder sizes, such as 42 Liters. The liquid litre size must then be converted to gas volume. For instance, when filled to 152 Bar of pressure, a cylinder that is 42 Liters (liquid) really contains 6.287 (or round to 6.3) CM of oxygen in a gas form (or 2200 psi).
Different oxygen plants have different capacity for producing oxygen. In order to concentrate oxygen for supply to hospitals or the industry, depending on the situation, it uses a technique that collects nitrogen from the surrounding air. The oxygen produced in this way can be delivered directly to the location of usage through a dedicated pipeline or compressed to fill cylinders.
The oxygen content of oxygen that is used in medicine ranges from 90 to 96 percent. The remaining gas primarily consists of nitrogen and argon.
Medkav's background
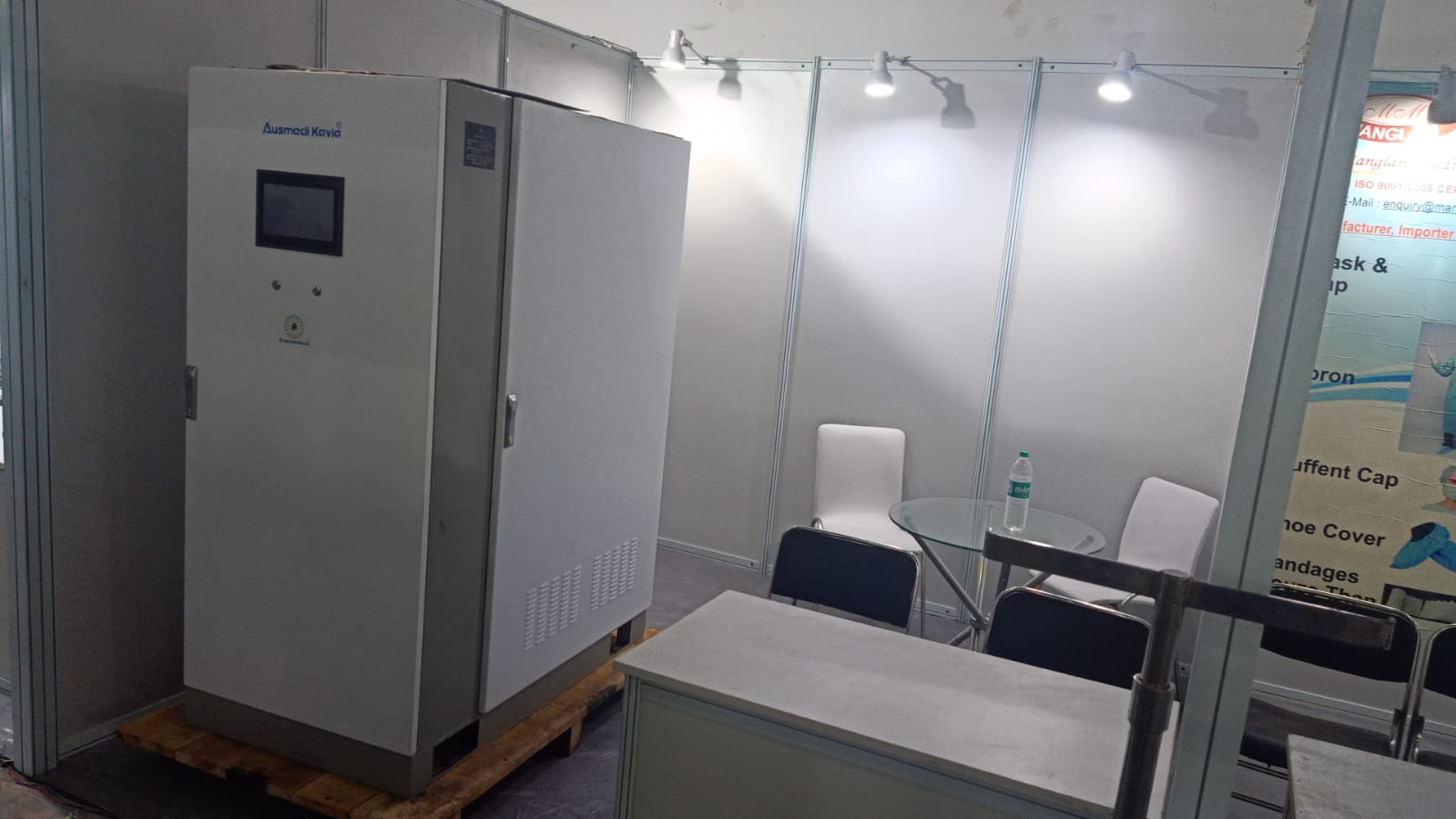
The facility's medical oxygen supply is maintained by Medkav's medical oxygen gas generator. By substituting long-lasting, high-quality oxygen generators for oxygen cylinders, we help hospitals save money. Our products are built to resist India's severe environment, power disruptions, and worries about air pollution. A major accomplishment might include making a technological leap. It will enter the market for commercial use more easily if it makes headway in this area. To disappear amid a sea of expectations is challenging, but not impossible.We have a number of strengths that enable us to help our clients resolve a wide range of service concerns at affordable prices. We do this by offering prompt and attentive service as well as a team of experts. Each client receives a single point of contact account manager from us as well. At their Bangalore Research Centre, our parent company, Kavia, manufactures products that are elegantly designed, painstakingly tested, skillfully produced, and expertly installed. These products are both safe and effective, as well as energy efficient and reliable.