We know that oxygen makes up 65 percent of the human body. Yes, oxygen is required for respiration, the process through which glucose is converted into energy. Every cell in our body, in fact, demands oxygen. When we take a breath, oxygen molecules enter our lungs and travel through the lung walls into our bloodstream.
Because COVID-19 inhibits pulmonary function, oxygen is essential for treatment. One of the most common symptoms in COVID-19 patients is shortness of breath or difficulty breathing. It also reduces the amount of oxygen delivered to various sections of the body. As a result, they require oxygen therapy, which can only be provided by medical oxygen.
Liquid Medical Oxygen is one of the ways that this oxygen can be delivered (LMO). LMO is high-purity oxygen created for usage in the human body and used for medical therapy.
Installation of liquid medical oxygen and various ways of supply have their own logistics, installation, and set-up procedures. As a result, the benefits and advantages of a liquid medical oxygen system vary based on the size of the hospital (bed capacity), its location, the amount of oxygen consumed, and local supply and service support. Medical oxygen supply systems for healthcare facilities are designed and installed according to specific requirements and criteria.
What Is The Process Of Making Liquid Medical Oxygen?
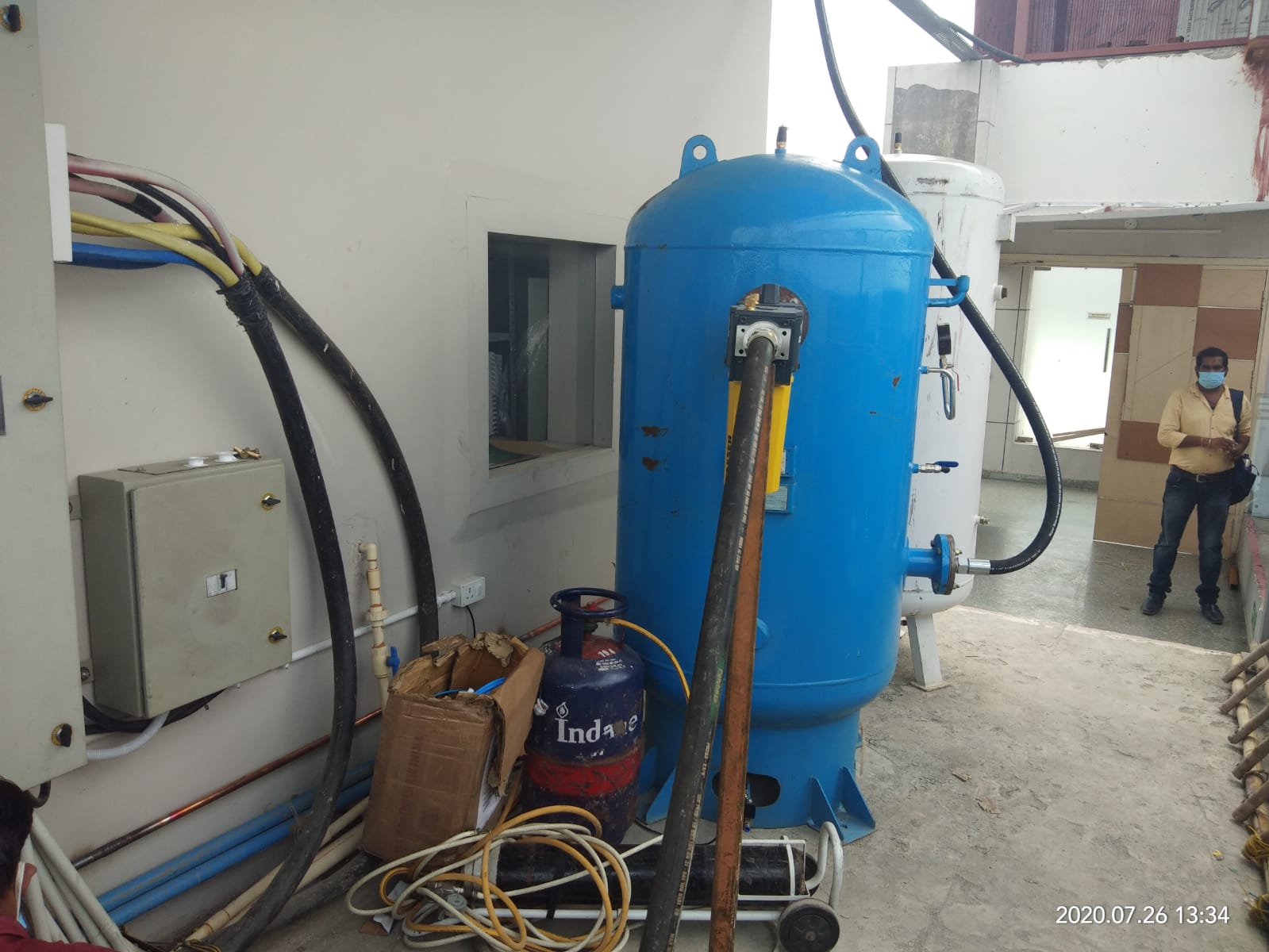
Separation of oxygen in Air Separation Units, or ASUs, is the most frequent technique of production. ASUs are essentially large-scale gas separation plants. They employ a technology known as fractional distillation to generate pure oxygen from atmospheric air, which is primarily composed of nitrogen and oxygen (78 percent nitrogen, 21% oxygen, and 1% additional gases such as argon, carbon dioxide, neon, helium, and hydrogen).This method involves separating gases from the air into distinct components after chilling them to a liquid state, and then extracting liquid oxygen from it.
The adiabatic compression test does not apply to liquid medical oxygen systems because they operate at less than 30 Barg, posing minimal risks, whereas in compressed gas supply systems, halogenated polymers in the components may catch fire due to adiabatic compression, releasing toxic fumes that could put the patient's life at risk. Because the product is made, transported, and supplied through highly O2 cleansed stainless steel cryogenic tanks, there is no risk of product contamination. However, because rust and dirt can flow with the gas, patient safety may be compromised.
Due to the unmanned functioning of the Liquid Medical oxygen system, social separation is feasible, something that none of the other ways of delivery can guarantee.
What Is The Purpose Of Liquid Oxygen?
Liquid oxygen is utilized as an oxidant for liquid fuels in missile and rocket propellant systems. For metal cutting, welding, scarfing, hardening, cleaning, and melting, oxygen is commonly used in conjunction with acetylene and other fuel gases. The majority of medical oxygen is manufactured in factories, of which India has roughly 500. They extract oxygen from air by chilling it to a liquid state and then separating the oxygen, nitrogen, and other components according on their boiling points.
Medical oxygen is critical for COVID-19 patients with severe symptoms. Liquid Medical Oxygen is one of the ways medical oxygen can be delivered (LMO). When the Covid-19 crisis struck, India had a severe shortage of liquid medical oxygen (LMO), and most affected patients required LMO care. The demand for LMO rose many times faster than expected, leaving many people stranded owing to a shortage of this vital substance.
In India, the LMO supply chain is moderately structured at the upstream production end, but very fragmented at the downstream end, where the manufactured LMO must reach the point of use at hospitals. The first bottleneck comes at the point of manufacture, where capacity is insufficient to meet the demands of Covid-19's increased demand.
LMO's Production Capacity
Let's now talk about how the Normal Plant differs from the PSA Oxygen Generator Plant and the standard one is referred to as a VSA oxygen generator.
In India, LMO production capacity is now around 7,000-8,000 tonnes per day. There is a capacity shortfall of available LMO in the country, with demand approaching 9,000-11,000 tonnes per day. The majority of LMO production (about 2,000-2,500 tonnes per day) takes place in captive units within large steel mills that require oxygen to enrich the blast furnace. LMO is now supplied by 33 steel factories in India. Only around 5-10% of the total gaseous oxygen produced by these steel factories can be transformed into LMO for use in the health sector.
TThe LMO is carried to the bottling factory in cryogenic tankers, where cylinders are filled with oxygen and subsequently given to hospitals. Tankers from steel mills are sometimes delivered directly to hospitals. The point of intersection between the LMO and cylinder supply chains is an example of a second bottleneck. The mismatch between the cycle time of LMO and the capacity of cylinders creates limits that make it difficult to meet demand.
Disadvantages:
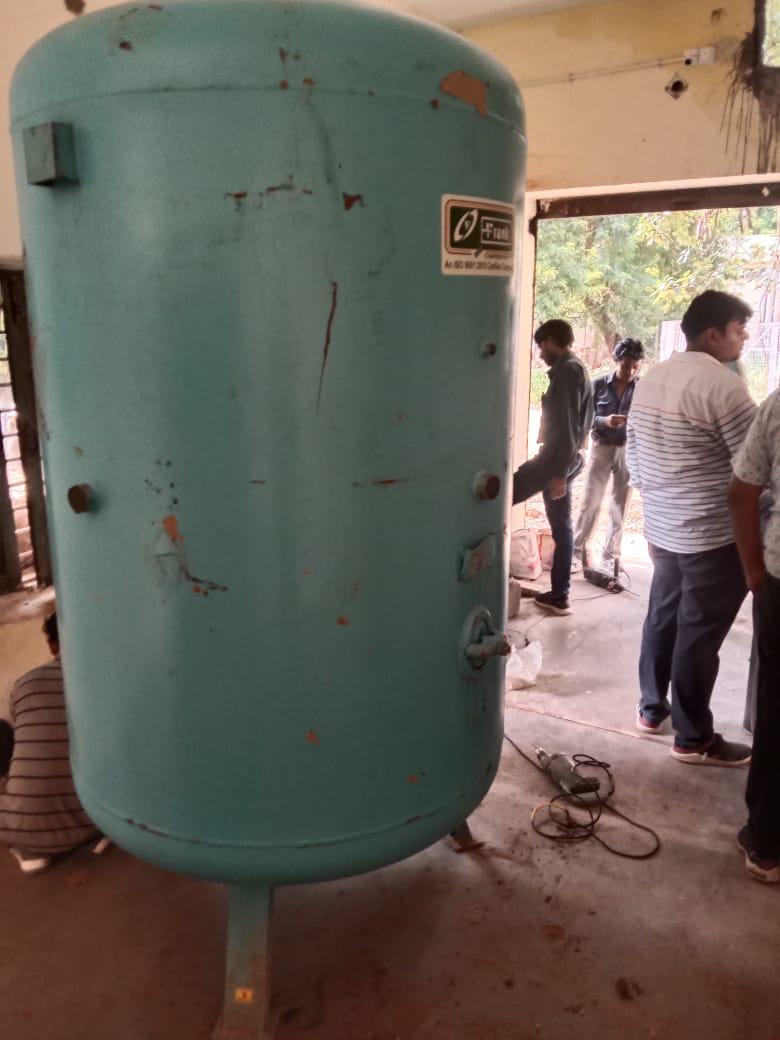
This is an expensive form of supplemental oxygen. Also, liquid oxygen cannot be stored for more than a week or two because it will evaporate. The tanks must be refilled often, requiring the scheduling of deliveries. In addition, the process of using the equipment has been described by some users as confusing and hard to remember.
⦁ Exposure to cold temperatures that can cause severe burns
⦁ Over pressurization due to the expansion of small amounts of liquid into large volumes of gas in inadequately vented equipment
⦁ Oxygen enrichment of the surrounding atmosphere
⦁ The possibility of a combustion reaction if the oxygen is permitted to contact a noncompatible material.
Background of Medkav technology
We assist hospitals, community clinics, healthcare centers, veterinary hospitals, and aquaculture businesses in India by bringing them state-of-the-art, 3rd and 4th generation advanced PSA technology. In conjunction with xxx, Hong Kong, we distribute, sell, service, and manufacture various varieties of oxygen generators and home oxygen concentrators (one sentence summary of our offering).Our parent company Kavia's products are elegantly developed, rigorously tested, professionally constructed, and set up at their Bangalore Research Centre, and are both safe and effective, as well as energy efficient and reliable. Medkav fully complies with ISO13485, ISO9001, and other national and international criteria.
Medkav products are widely known and appreciated in medical institutions around the world due to their technical superiority, high reliability, and competitive performance-price ratio. We collaborate with well-known domestic and international suppliers.
Our partnership is a journey, not simply an event, and it is tailored to the customers' current and future needs. We provide world-class service (USP) Unlike most other companies (current market alternatives/competitors), we provide prompt and attentive service, a team of experts with diverse strengths to assist our clients in resolving various types of service issues at reasonable prices, and a dedicated single point of contact account manager to service each client.